latest news
The importance of annual fall protection inspections
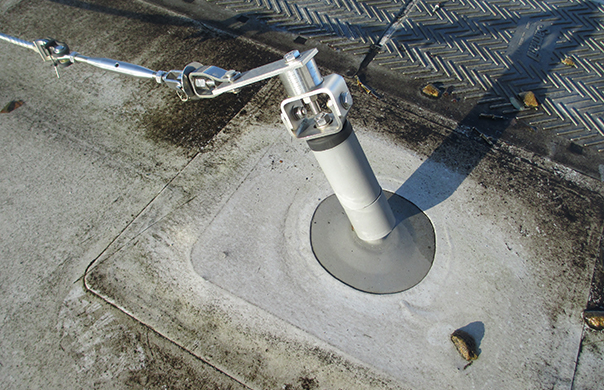
By Mark Dolan, General Manager, Roof Edge Fabrications
Last week I started this Blog series on inspection of fall protection systems with an overview of your duties when it comes to maintenance of equipment. This week I’m going to look at fall arrest and restraint systems and explain why it’s important to have these inspected regularly and certified annually by a competent person.
What are fall arrest and fall restraint?
According to the work at height hierarchy of control, fall arrest and restraint systems should only be used as a last resort. This is because they provide individual safety protection so are totally dependent upon the worker using the equipment correctly.
These systems generally consist of an anchorage point, a lanyard and a full body harness. When used as fall restraint the lanyard will be a fixed length to prevent the user reaching a fall risk.
What can go wrong?
Systems can often be removed, damaged, tampered with or even deployed. For example, the rubber underside of the weights on a portable anchorage point may be damaged or removed. This rubber is a critical part of the system as it not only prevents damage to the roof but it also increase the frictional tension of the anchorage system. If the rubber is missing the system could move significantly when arresting a fall. Whenever a system has been used to arrest a fall it must be immediately taken out of action as once deployed it’s no longer safe to use.
Any fall protection system should be visually checked before each use and recertified by a competent person on a regular basis. The frequency of recertification depends upon the system, how often it’s used and the environment. As a general rule we recommend that recertification is carried out at least every twelve months.
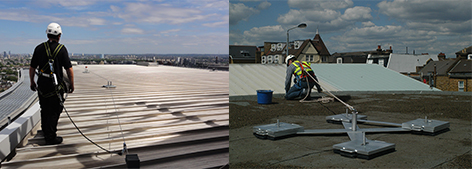
What should you look for?
Competent inspection and rectification of equipment should include the following areas:
- a detailed inspection of the structural connection of the system such as posts and end anchors to make sure they’re secure
- pull testing of swage terminations as outlined in the manufacturer’s recommendations
- pull testing of all visible end fixings to concrete/brickwork/ structure
- checking that the system runs smoothly over all intermediate brackets
- inspection of all shock absorbers
- examination of the cable for any damage, kinks or signs of wear
- checking and tightening of all accessible fixings
- checking for any signs of corrosion to galvanised components
- re-tensioning of the cable if required
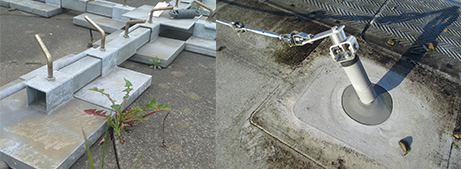
Don’t forget the PPE
All PPE used with the system must also be inspected and checked that the different items are compatible with one another. PPE should be inspected prior to each use, but more detailed inspections are required at least every six months. PPE inspection should include the following:
- inspecting lanyards and harnesses for signs of damages such as cuts, stains, fraying or breaks in stitching
- checking for damage to fittings (e.g.karabiners, screwlink connectors, scaffold hooks)
- checking for damage to the sheath and core of a kernmantel rope
If the PPE is used more frequently, then interim inspections would be required every three months.
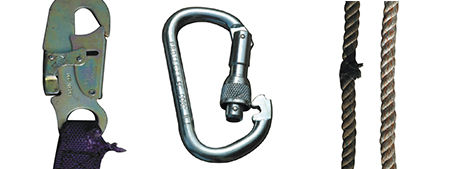
Inspection Regime
Fall arrest and restraint systems are vital pieces of equipment when working at height so it’s essential that they’re safe to use at all times, and the best way to do this is to introduce a regime whereby they’re inspected and recertified at least annually by a competent person.
Next week I’m going to look at collective protection such as guardrails and discuss why these also need to be part of your recertification regime.